There are a range of pros – and cons – to understand behind each weld technology option for your mission-critical application
The last thing you want is a weld joint that negatively impacts the performance and reliability of your product. Choosing the wrong welding technology for your application can cause significant consequences: weak joints that fail under stress, excessive heat distortion that ruins precision components, or contamination that compromises material integrity. Beyond the immediate costs of rework and replacement, improper welding can create catastrophic failures in critical applications, compromise structural integrity, affect corrosion resistance and create dimensional inaccuracies that cascade through assemblies.
In medical, aerospace, electronics or pressure vessel applications, these failures potentially endanger lives and always threaten your company’s reputation. Meanwhile, the financial impact extends beyond simple repairs to production delays, warranty claims and liability issues. Each of these failures translates to increased costs and potentially compromised product safety, underscoring why selecting the appropriate welding technology is anything but a casual after-thought.
![]() |
White PaperWhat to Know About TIG vs. Electron Beam Welding |
As a welding services partner, many customers come to EB Industries without really knowing which of our range of weld technologies is best for their project. And, because we offer everything from MIG/TIG to electron beam, laser welding and laser hermetic sealing, all under one roof, we can make recommendations without bias that pushes people to just whatever tool we may happen to offer.
Let’s consider the three primary weld technologies used for most precision welding projects, and review the various advantages of each as a way to begin to identify what’s best for your project.
Electron Beam Welding
Precision and Depth in a Vacuum Environment
Electron Beam welding utilizes a focused stream of high-velocity electrons to fuse materials. Conducted within a vacuum chamber to prevent electron scattering, this process ensures high-purity welds with minimal contamination. The kinetic energy of the electrons converts to heat upon impact, causing high-precision melting and joining of the metals. Figure 1 illustrates an EB weld and shows that the weld can penetrate deeply into a metal.
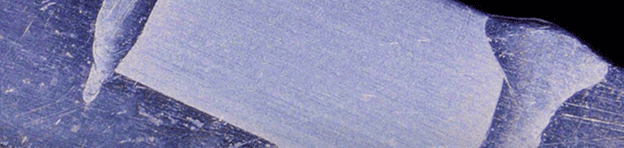
Advantages:
- Exceptional Precision: EB welding allows for meticulous control over weld penetration, ranging from as shallow as 0.001 inches to depths of up to 2 inches.
- Minimal Heat Affected Zone (HAZ): The high depth-to-width ratio results in a narrow HAZ, reducing material distortion and preserving the integrity of adjacent components.
- High Weld Strength: Welds produced can retain up to 95% of the base materials’ strength, ensuring robust and durable joints.
- Purity and Cleanliness: The vacuum environment eliminates impurities such as oxides and nitrides, resulting in exceptionally clean welds suitable for critical applications.
Applications:
EB welding is the optimum solution for projects requiring deep, precise welds with minimal thermal impact. It’s highly effective for joining dissimilar or refractory metals that are challenging to weld using conventional methods. Industries such as aerospace, medical device manufacturing and electronics frequently leverage EB welding for components where weld integrity is paramount.
Considerations:
The necessity of a vacuum chamber can limit the size of workpieces and may require specialized fixturing. Additionally, the initial setup costs can be higher when compared with other welding methods, but the precision and quality justify the investment for many applications.
Laser Beam Welding
Speed and Precision Without the Vacuum Requirement
Laser Beam welding employs a concentrated, high-power laser beam to melt and fuse materials. This non-contact process does not require a vacuum environment, allowing for greater flexibility in production settings. The precision of the laser enables high-quality welds at impressive speeds. Figure 2 shows a precision weld joint.
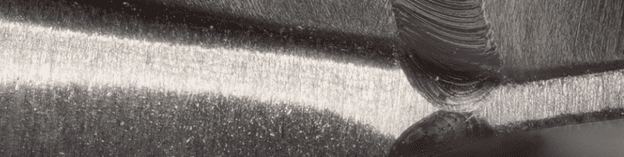
Advantages:
- Controlled Penetration: Weld depths can be precisely managed, ranging from 0.005 inches to 0.25 inches, accommodating a variety of material thicknesses.
- Micro-Welding Capability: LB welding precision makes it ideal for welding very small or thin components, such as foils, stents, and sensor diaphragms.
- Low Thermal Input: Pulsed lasers minimize heat application, protecting sensitive components and reducing the risk of thermal distortion.
- Versatility: LB welding can effectively join dissimilar and crack-sensitive materials without requiring a vacuum, facilitating faster production cycles.
- High Production Rates: With feed rates up to 200 inches per minute, LB welding is well-suited for high-volume production environments.
Applications:
LB welding is optimal for applications necessitating pinpoint accuracy and high-speed production, such as in the medical device, automotive, and electronics industries. The technology is particularly beneficial for welding thin materials and small components where precision is critical.
Considerations:
While LB welding offers high speed and precision, it may not be suitable for thicker materials requiring deeper weld penetration. Also, like EB welding, the size of the piece that LB welding can operate on is limited.
Tungsten Inert Gas (TIG) Welding
Versatility and Aesthetic Quality
TIG Welding, also known as Gas Tungsten Arc Welding (GTAW), utilizes a non-consumable tungsten electrode to produce the weld. High voltage through the tungsten electrode forms an arc with the metal at the weld site. A filler rod provides the weld material. An inert shielding gas, typically argon or helium, protects the weld area from atmospheric contamination, resulting in clean and high-quality welds. Figure 3 illustrates the versatility of TIG welding by showing the technology used on a complex structure.
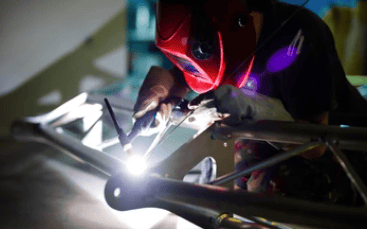
Advantages:
- Dimensional Versatility: TIG welding allows the welding of any size vessel, pipe, or other structure, which does not require fixturing to hold an object.
- High-Quality Welds: TIG welding produces clean, precise, and aesthetically pleasing welds with minimal spatter, making it ideal for applications where appearance is important.
- Positional Flexibility: TIG welds can be performed in any position to allow welding joints with limited accessibility.
- Fills Large Weld Gaps: When large spaces exist between two parts, TIG welding is the superior method for forming a strong, reliable weld.
- Weld in Any Location: TIG welding can be performed in the field as well as in a manufacturing facility.
- No Filler Material Needed: For certain applications, TIG welding can be performed without filler material, reducing costs and simplifying the process.
Applications:
TIG welding enables welding on large and complex structures. TIG welding also allows difficult-to-access joints to be welded. On large structures in the aerospace, automotive, and energy industries, TIG welding produces clean, high-quality welded joints.
Considerations:
TIG welding is generally slower and more labor-intensive than other welding methods, which can increase production time and costs. It also requires a higher skill level from the operator to achieve optimal results.
Using Multiple Technologies
In some cases, your application may require multiple welding technologies. Figure 4 shows an example in which two welding technologies are employed. The structure is a vessel with a flange on one side and an eye bolt on the top. Both the eye bolt and the top cover of the vessel can be laser welded to the chamber. Laser welding allows precise control of weld penetration, minimizes the applied heat, and does not require a vacuum. Since the vessel is too large to be fixtured, TIG welding is the most appropriate technology to weld the flange.
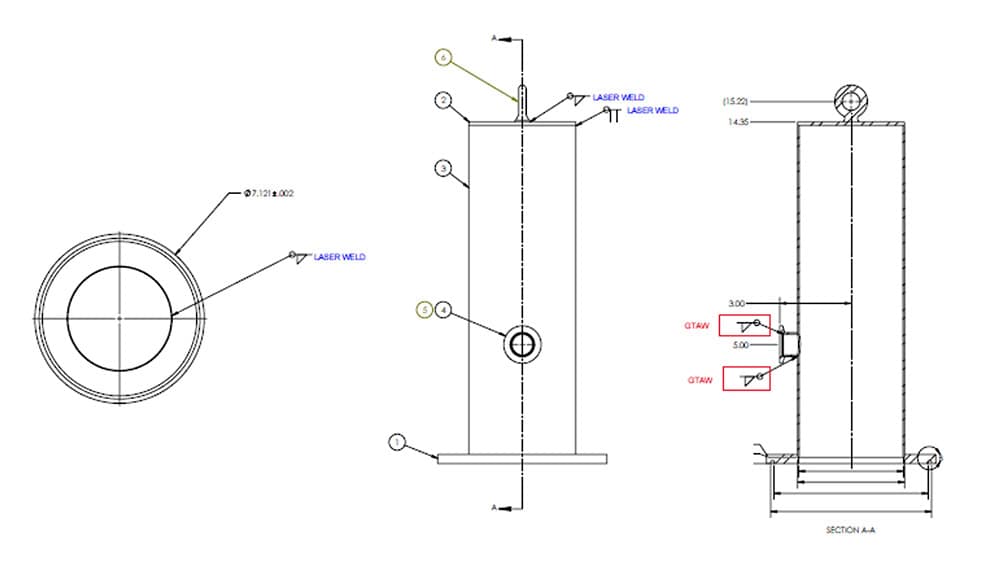
Why Partner with EB Industries
EB Industries brings more than 60 years of precision welding expertise to your most challenging applications. Our comprehensive approach includes advanced technology with electron beam, laser, and TIG welding, supported by experienced welding engineers to help select the optimal process. We maintain rigorous quality assurance with compliance from ISO to NADCAP to MIL-SPEC standards
As a complete solution provider, we offer services from design assistance to pre-processing and post-processing services. Our mission-critical focus specializes in applications where failure is not an option. We are committed to performance, precision, and partnership that ensures your welding projects meet the highest quality standards while delivering on-time results—even for rush jobs.
Pre- and Post-Processing Services
Beyond our core welding capabilities, EB Industries offers comprehensive support services. Our pre-processing services include:
- CAD/CAM product design and weld design
- Tooling design and fabrication,
- Part cleaning and assembly
- Strategic sourcing
- Subcontractor contract management.
For post-processing, we provide:
- Metallurgic evaluations
- Leak testing
- Destructive and non-destructive testing
- Post weld thermal treatment.
Find Your Optimal Welding Solution
Avoid the risk and the costs of using an improper welding technology that could compromise the structural integrity and performance of welded components. Read more in our comparison chart on various weld technologies. Or, contact EB Industries today to discuss your specific application needs with our expert team of welding engineers. We’ll help you navigate the complexities of welding technology selection to ensure the reliability of your product.
Visit: https://ebindustries.com