Overview
Fine leak testing is, as the name implies, a testing method used when very small leaks need to be detected in parts and electronic packages that are hermetically sealed. Failure of a hermetic seal can result in moisture or other contaminants damaging the integrity of the part or package, which poses problems in both the short and long term. Proper fine leak testing is essential to ensure the quality of the hermetic seal and the integrity of the packaging.
Testing Process
The part to be tested is filled with helium and placed in a testing environment. A helium mass spectrometer is then used to measure the volume of helium that passes through the hermetic device each second under a pressure difference of 1 atmosphere. Helium molecules are very small and will reveal leaks that other processes typically cannot find.
The units of measure in helium leak testing are typically in the range of 1 x 10-6 to 1 x 10-10 cc of helium per second or air equivalent. The harsher the environmental and functional conditions, the lower the leak rate must be to ensure the part will survive for the duration of its lifetime. There are different governing specifications for different products:
- Electronic Packages: MIL-STD-883 Method 1014 , MIL-STD-202 Method 112 or MIL-STD-750 Method 1071.6
- Hybrid Packages for Space: MIL-PRF-38534
- Non-Electronic Devices: MIL-STD-810
- Chemical Munitions: MIL-STD-1441
Advantages and Disadvantages of Fine Leak Testing
Fine Leak Testing has many advantages. It is a very fast test requiring simple or no tooling, which is why it’s often chosen as the key test method in production applications where quick turnarounds are necessary. The testing process also doesn’t leave behind any residue, minimizing the potential for contamination and FOD (foreign object damage), which are hazards posed by some other test methods. Fine Leak Testing is also easy to automate, which, again, makes it a great choice for use in production. At EB Industries, we can program the amount of helium and the duration of time that our welds are exposed to it, as well as monitoring the measurement of the leakage. This allows our technicians to expeditiously test welds and quickly turn around jobs.
Fine Leak Testing isn’t for every application. One disadvantage is that the testing is typically done at 1 ATM (14.7 PSI or 760.21 Torr), which may not be sufficient for high-pressure applications, in which case, it might be required to perform high-pressure helium leak testing. Another disadvantage is that Fine Leak Testing may not detect a large leak in a smaller sealed device, in which case gross leak testing might be required. Lastly, the cost of the equipment can be prohibitive. Helium mass spectrometer devices typically cost an order of magnitude more than equipment used for pressure or volume decay testing. As Fine Leak Testing is a critical process in a lot of our welding applications, we have three systems in-house so that we can run tests in-line with our welding processes.
Typical Applications
Hermetically sealed microelectronic packages that require a low moisture environment (typically specified to be less than 5000 ppm) to prolong the life of the device in space or in an aircraft where repeated altitude cycling will produce condensation.
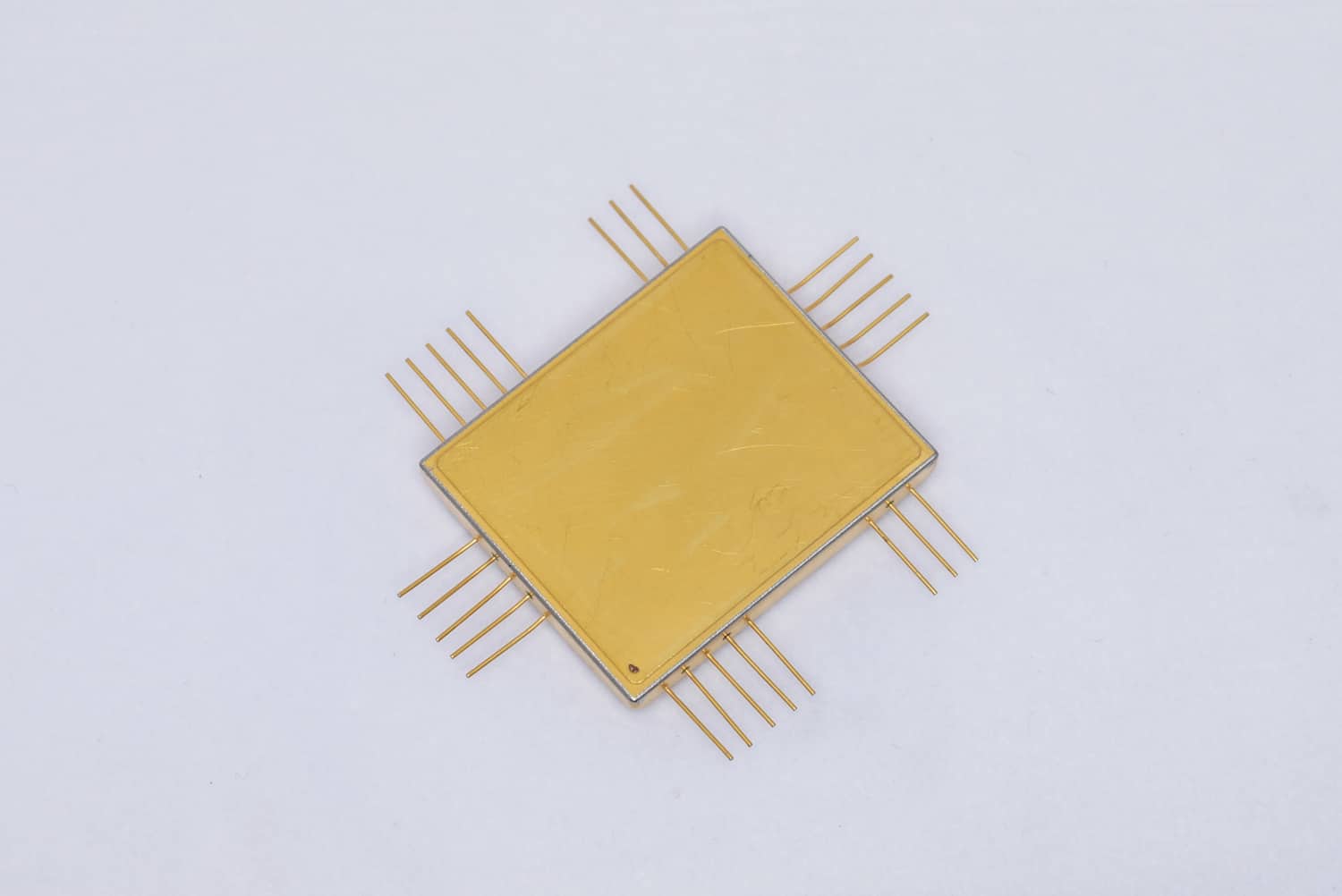
High vacuum applications where a very small leak over time will degrade the performance of a device or system. Some examples of this are microchips, solar panels assemblies, and particle accelerator components. A very common family of parts that requires leak testing are cold plates, which are used to draw heat away from sensitive components, such as microchips, computer processors, etc.
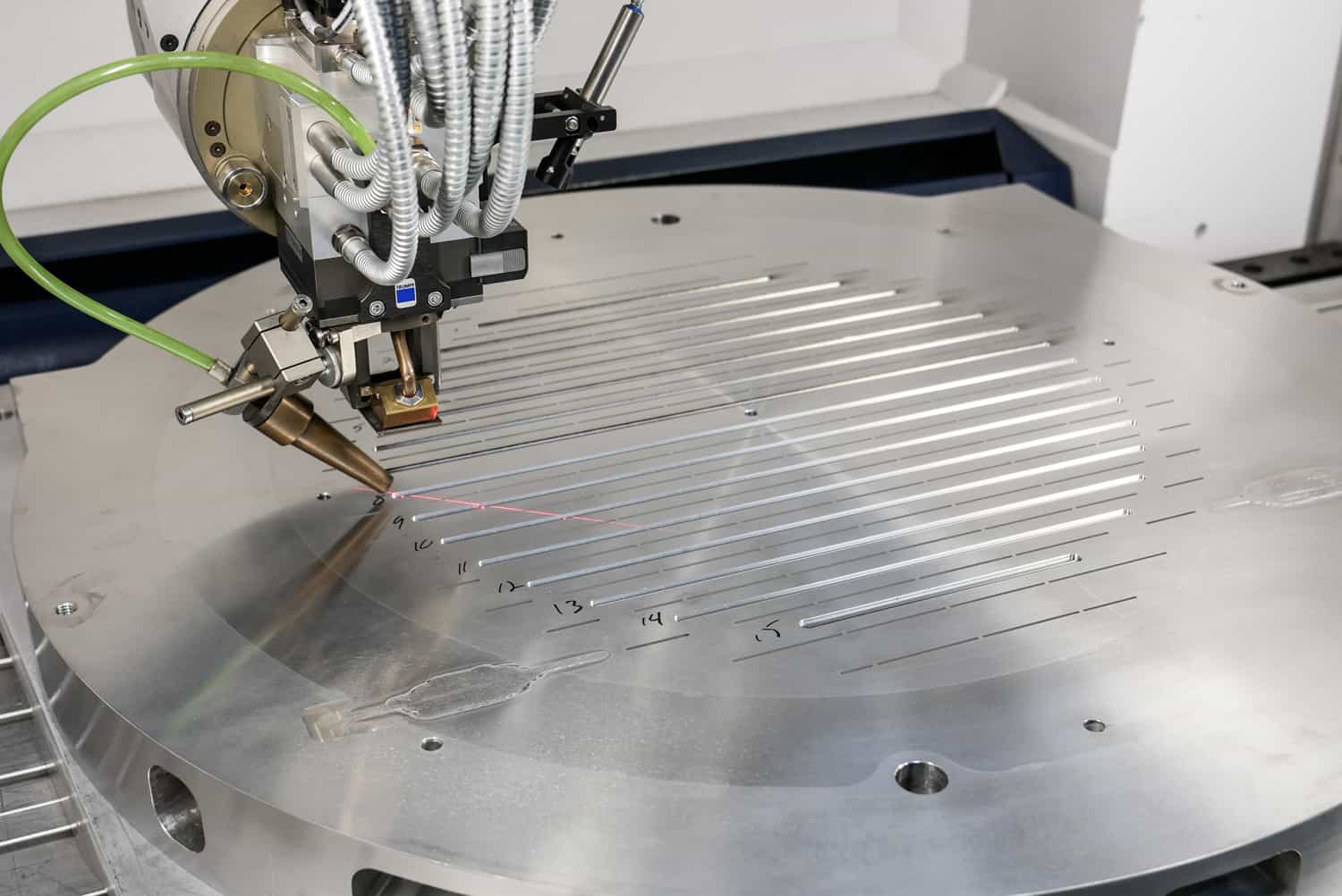
Implanted medical devices such as heart monitors, heart pumps, and pacemakers. Small leaks in these applications could be a matter of life and death, hence fine leak testing is essential.
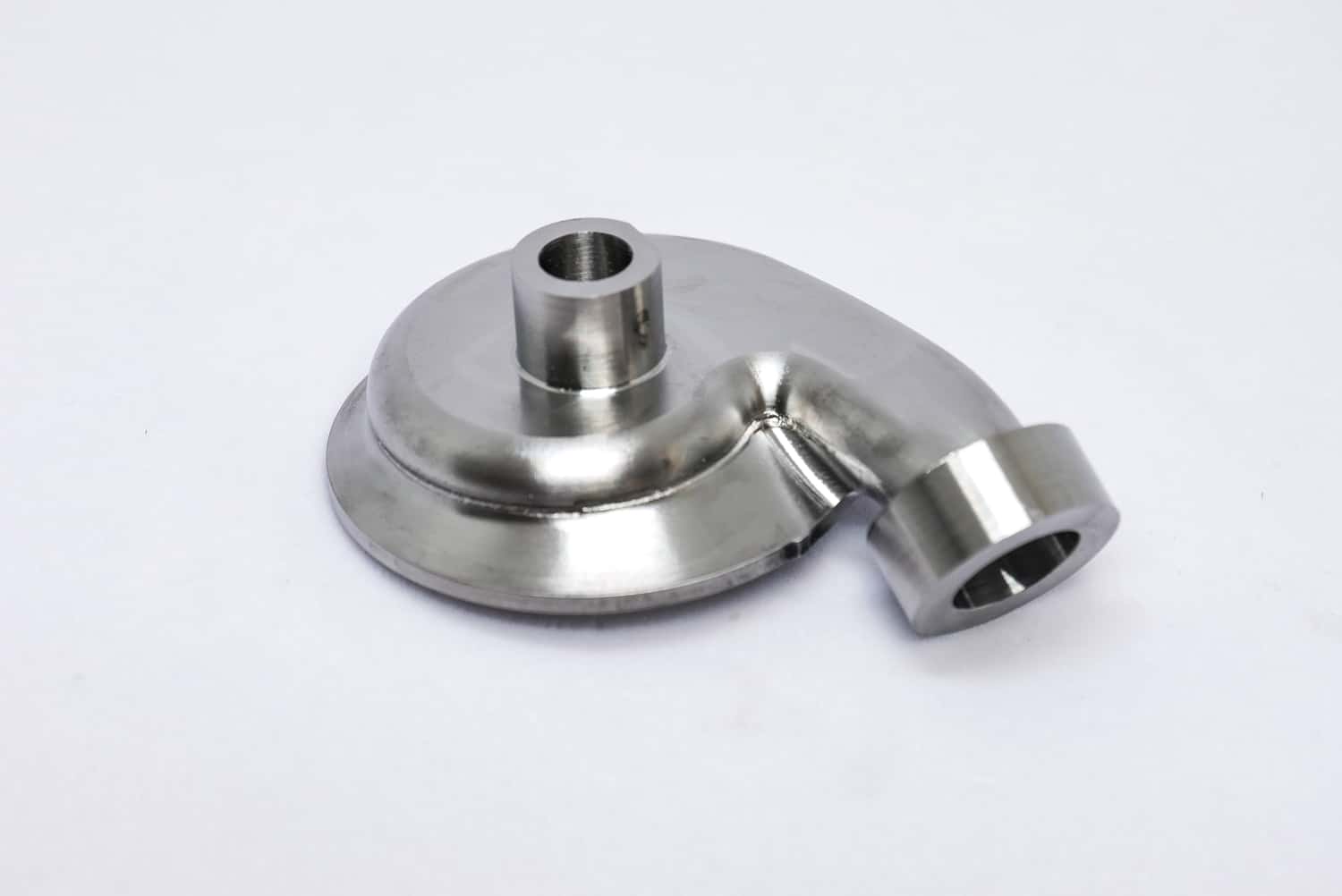
Any application where a rapid test which requires no cleaning can be used in production lines to improve throughput over other methods, such as pressure decay, volume decay and bubble testing. This sort of testing is commonly found in automotive and marine industries as well as in aerospace fuel system applications and hydraulic system testing.
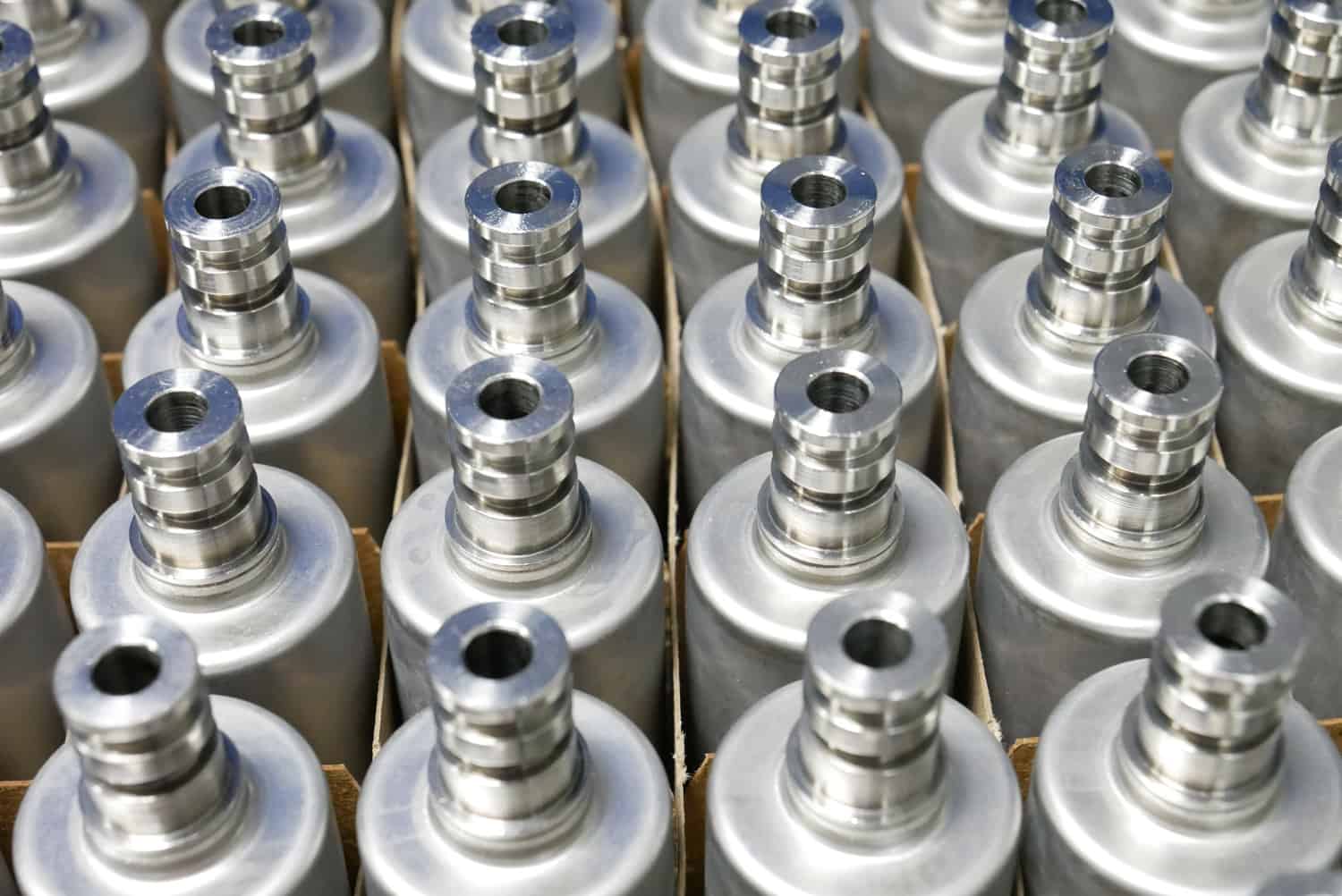
Conclusions and Next Steps
We offer Fine Leak Testing for hermetic sealing projects, as well as any application where the process is called out in a specification or required by a customer. Please contact us if you need more information regarding leak testing or have questions regarding your particular project or part.