What is the principle of laser welding and how does a laser welding machine work?
A laser beam is generated by rapidly raising and lowering the energy state of a “optical gain material,” such as a gas or a crystal, which causes the emission of photons.
The photons are subsequently concentrated and made coherent (lined up in phase with each other) and then projected on the surface of a part where radiant heat “couples” with the material, causing it to melt and produce the weld. Unfortunately, the majority of the laser’s power is wasted on heat and reflected off the part’s surface. Thus, by contrast, the depth penetration per unit of power in a laser weld is less than that of an electron beam weld. This problem can be mitigated by pulsing the laser, i.e., varying the power of the laser during the weld cycle. Pulsing the laser lowers the average power during the weld cycle keeping the part relatively cool. This can be particularly beneficial in achieving a strong weld on highly reflective materials such as copper and aluminum.
The power output of a laser can vary from a few watts to hundreds of kilowatts, and different types of lasers have different welding characteristics. As an example, the particular wave- length of light produced by the laser can make it more suitable for some applications and less for others.
Laser welding generally requires the use of a cover gas to keep oxygen out of the weld area improving efficiency and weld purity. The type of gas used depends on the type of laser, the material being welded, and the nuances of the application. Some laser welding applications may require an enclosed environment (i.e, a “glove box”) to assure complete gas coverage when joining parts having complex geometries.
Which industries can laser welding machines be used for?
Laser welding has many applications throughout a varied group of industries including the aerospace industry, electronics manufacturing, medical device fabrication, pipeline industry, hardware manufacturing, battery industry, homebuilding materials industry (like lighting, kitchenware, and building materials), the mold and machinery manufacturing industry, automobile manufacturing, jewelry industry, and the semiconductor industry.
What is laser welding used for?
Laser welding is used in several industries for specific applications including:
- Automotive Industry – Used for joining components like body panels, exhaust systems, fuel tanks and even batteries for electric vehicles.
- Aerospace Industry – Turbine blades fuselage sections, engine parts, sensors and similar assemblies.
- Electronics Manufacturing – Used to weld microelectronic components, fine connections in circuit boards and to seal electronic housings.
- Medical Industry – It’s used extensively in this industry with some common applications like surgical instruments, implantable devices and within medical equipment.
- Semiconductor Processing – This is one of the quicker growing areas for laser welding to assemble semiconductor packages, sensors within microchip printing machines and in magnetized assemblies used in various stages of semiconductor processing.
What kind of application usually uses laser welding?
Laser welding is used in applications where precision, speed and versatility are required. EB Industries services primarily the aerospace industry, electronics manufacturing, medical device fabrication, and the semiconductor industry.
Can a laser welder weld aluminum?
It’s difficult to laser weld some alloys of aluminum due to the high reflectivity and crack sensitivity of these materials. EB Industries utilizes proprietary technology to be able to overcome these challenges. Learn more at
Laser Welding Aluminum.
What materials can a laser welding machine weld?
Laser welding can weld titanium, aluminum, stainless steel, iron, kovar, molybdenum. Learn more about each material below:
What are the main types of laser welding machines?
One of the core decisions to be made is whether the weld process will use a continuous wave laser or a pulsed laser.
Continuous wave (CW) lasers are lasers that emit a constant, uninterrupted beam. They are usually Fiber style lasers that use diodes switched on to excite a gain medium, thus outputting laser light. CW lasers are especially suitable for deep penetration welds (over .060” deep), and welding crack sensitive materials like high carbon stainless steels.
CW lasers can be run at power levels as low as 200 Watts to as high as 100,000+ Watts. CW laser welding requires 200 watts or higher to successfully couple most metals. This wide power range, mixed with high energy densities, aids in fusing metals with different thermal and reflectivity characteristics. For example, ferrous metals, such as stainless steel, couple at lower power (roughly 200w), while materials like aluminum and copper couple at significantly higher power (600-800w).
CW lasers usually run at high feed rates to prevent overheating the part. Typical CW feed rates are around 100 inches per minute. Power and feed speed must be precisely balanced to obtain a weld with the specified penetration. The slower the feed rate, the deeper the penetration and the more heat applied to the part.
Pulsed lasers produce a series of short pulses at a certain width and frequency. A pulsed laser can produce a peak power that is greater than its average power because energy is stored up in capacitors before it is released. Pulsed lasers are capable of very high peak powers: a 25 W pulsed Nd:YAG laser can produce peak powers up to 5 kW for a few milliseconds. This means it can produce a spot weld that would require a CW laser sized at 5 kW!
With pulsed lasers, a seam weld is created by a series of overlapping spot welds. For hermetic sealing applications, these spot welds are overlapped between 80-90%. For simple structural welds that do not need to be sealed, the overlap can be relaxed to around 70%.
Due to the short duration of the pulse (typically a few milliseconds long), heat entering the part is minimized, making pulsed laser welding recommended for use around heat sensitive components and very thin-walled materials.
Pulsed laser welding tends to work well with reflective metals due to the high amounts of energy delivered at the onset of the pulse. Often referred to as an “Enhanced Pulse,” this spike of power at the beginning of the pulse cycle only lasts a fraction of the total pulse duration. However, it is powerful enough to break past the reflectivity of the material, while keeping the average power low, which reduces heat. A CW laser would have to deliver a lot of energy to couple a very reflective metal, and the resultant heat could easily damage the part or components inside of it.
Frequently Asked Questions
Is an electron beam the same thing as a laser?
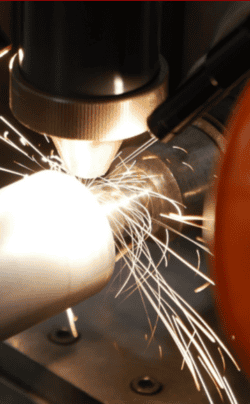
A laser beam is generated by rapidly raising and lowering the energy state of an “optical gain material,” such as a gas or a crystal, which causes the emission of photons.
The photons are subsequently concentrated and made coherent (lined up in phase with each other) and then projected on the surface of a part where radiant heat “couples” with the material, causing it to melt and produce the weld. Unfortunately, the majority of the laser’s power is wasted on heat and reflected off the part’s surface. Thus, by contrast, the depth penetration per unit of power in a laser weld is less than that of an electron beam weld. This problem can be mitigated by pulsing the laser, i.e., varying the power of the laser during the weld cycle. Pulsing the laser lowers the average power during the weld cycle keeping the part relatively cool. This can be particularly beneficial in achieving a strong weld on highly reflective materials such as copper and aluminum.
Is laser welding as strong as MIG?
Will laser welding replace MIG welding?
Is laser welding as strong as TIG welding?
What is the disadvantage of laser welding?
Laser welding also isn’t great for some dissimilar metal combinations. EB Industries has invested in proprietary technology that allows us to weld dissimilar metals and difficult to weld materials.
Laser welding can’t achieve the same depth of penetration as a process like electron beam welding due to the reflectivity. Technology is expanding to improve this but it’s not at the same level as other welding methods yet.