Physical weld testing is used to test and measure the mechanical strength of the welds involved in an assembly. These methods focus on comparing pre and post-weld conditions, such as torque and tensile strength as well as ductility, and focus on properties of welds that visual inspection, helium spectrometer fine leak testing, dye penetrant and radiographic inspection typically can’t reveal.
Three common test methods EB Industries uses to measure physical characteristics of the weld and base metal are torque testing, tensile testing and bend testing. Each test method is controlled by specific specifications, but AWS B4.0 discusses each of the mechanical tests as well.
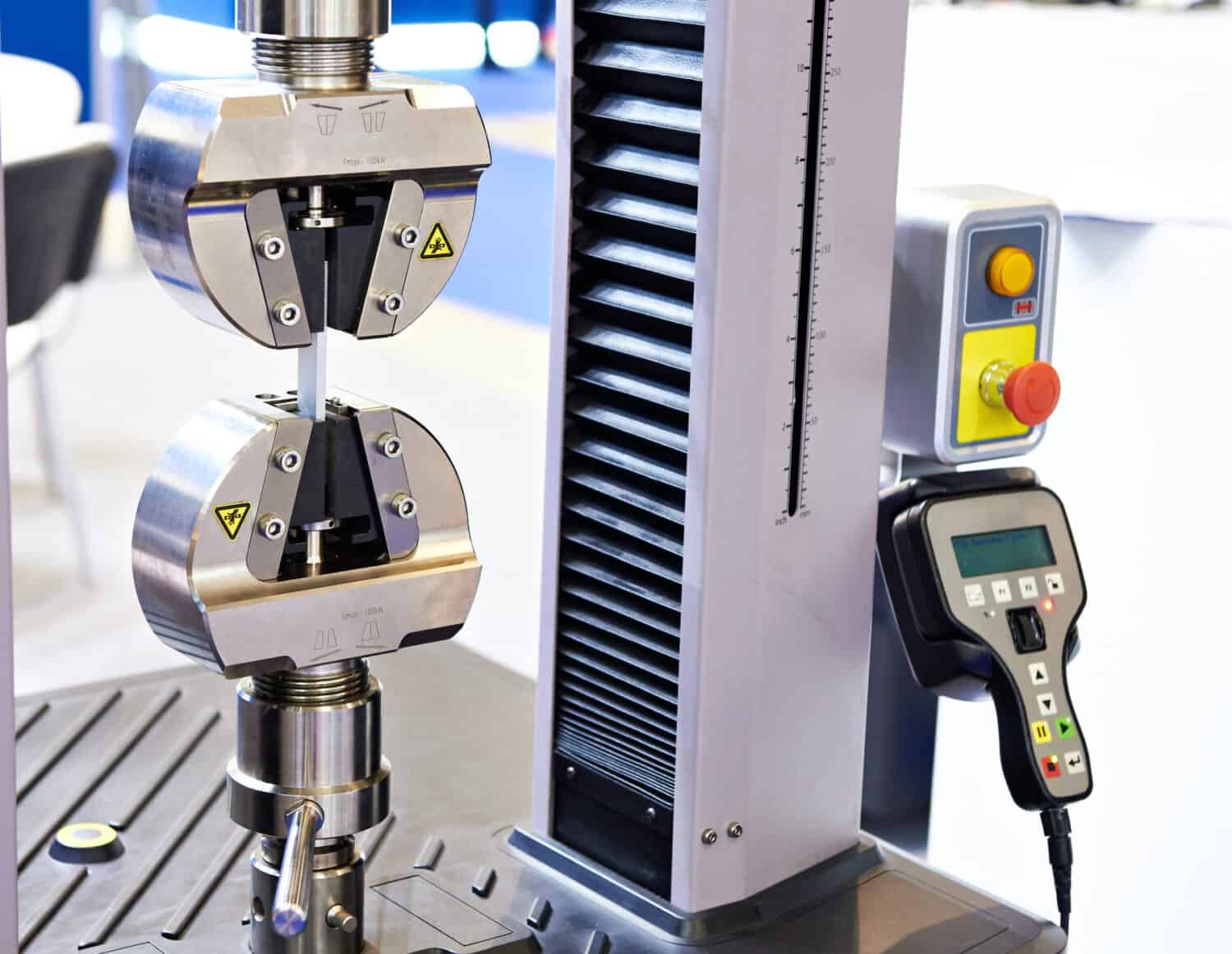
Torque Testing
Torque testing is used to measure the retention of torque strength after welding. This test reveals how much strength was gained or lost between the base metal and the weld after welding has occurred. The units of measurement for this are either foot-pounds (ft-lbs) or Newton-meters (Nm). The details regarding how to perform a torque test, the equipment required and the frequency at which the test should be performed are contained within the specification ASTM D2063.
A torque test is simple: a torque wrench is fitted to the welded component and then tightened until either the weld breaks and the components separate or until a specified measurement that indicates the minimum requirement is reached. The important thing to note is that the assembly needs to be configured so that there is a component on which the torque wrench can be affixed. An example of a part design that allows for this testing is shown below:
One advantage of this test method is that it can be used to evaluate weld penetration without sectioning a part. In many cases, penetration is calculated to provide the amount of strength required to keep the assembly functional while in its intended use. If the torque test doesn’t break the assembly at the specified minimum, it can be concluded that the necessary penetration has been achieved.
Torque testing is simple and quick to perform, and typically involves just the welded assembly and a calibrated torque wrench, which makes it a very production-oriented process as compared to other testing methods. One disadvantage of this process is that the location where the torque wrench grabs the part can be damaged, which may negatively impact the integrity of the assembly. Additionally, there are instances where the part must be tested to failure, which makes torque testing destructive. In situations where only a minimum torque strength must be met, parts can be tested and still used in production. If the requirement of the test is meeting a minimum torque amount, 100% of the parts can be tested instead using AQL sampling.
Tensile Testing
Tensile testing is used to measure the strength of a welded joint. The procedure and measuring methods are discussed in ASTM E8.
First, the area of the location to be tested is calculated by multiplying the width and thickness.The specimen is then placed in a machine capable of pulling with the strength required to break the sample. As the sample is pulled, the force applied is measured using a calibrated gauge. When the sample breaks, the tensile load is recorded and then tensile strength is calculated using the formula shown below. Tensile strength is typically measured in pounds per square inch (PSI), and the most commonly accepted criteria for this test is that the specimen shall not pull apart at less than 90% of the tensile strength of the base metal.
Tensile testing can indicate if the welding process negatively impacted the material in the weld zone or around it. This advantage is why tensile testing is typically used when comparing materials and in the process of alloy development.
A disadvantage to this method is that, depending on the final assembly configuration, generally it can only be conducted on sample parts. As can be seen in the figure, the tensile test specimen is usually a rectangular strip of material with a weld in the middle — a bit simple for a production parts design. Tensile testing also requires specialized tooling and equipment that a torque test doesn’t require. Finally, like a bend test, tensile testing is destructive as you are stressing the sample until it breaks, which renders this testing method unsuitable for production assemblies.
Bend Testing
Bend testing allows for the inspection of the quality of the weld metal at the face and root of the weld, as well as the amount of penetration achieved. ASTM E190 dictates the procedure and the equipment required to perform bend testing. The sample being tested is welded and then a strip of metal of a specified length is cut from the sample. This is then bent into a U-shape that approximates the minimum percent elongation required in a comparable tensile test. If there are issues within the weld, the material will break in those problematic areas. If the break(s) exceeds a predetermined limit, the sample is rejected. This test is measured in either millimeters (mm) or inches (in); the defects need to be measured to ensure that they don’t exceed the maximum allowed limits. The image below shows a sample before and after a bend test:
One advantage of this method is that when a sample is subjected to localized overstressing (the bend test), defects can be revealed that won’t necessarily appear in an x-ray inspection. A bend test reveals defects not shown by X-rays — the welded area may be weakened in a manner that can’t be seen in an X-ray, but breaks before reaching the minimum requirement of the bend test.
Bend testing is also an efficacious method for qualifying welders and processes, rather than using a process like radiographic inspection, which typically requires a shop to contract with an external lab. Bend testing is relatively easy and inexpensive to perform in-house.
A major disadvantage of bend testing is that usually it cannot be performed on a production part, and requires the use of specifically designed and constructed samples. The only exception to this is if the production assembly is rectangular, perhaps machined from plates or pipes. That’s why it’s more commonly used for qualification than in production. This is also a destructive testing method and parts can’t be used after testing, another reason why it is a less common method of weld testing than torque testing.
Summary
At EB Industries, we perform all of these physical tests as per your requirement. We can help you design assemblies for this purpose if the production parts can’t be utilized for testing. Please contact us if you need any additional information regarding these test methods or if you have a need for these services to qualify or accept your welded assemblies.